China’s tightening of rare earth magnet exports has pressured the global automotive industry tremendously. Since rare earths are essential materials for core components of electric vehicles, and China controls 70% of the world’s minerals, 85% of refining capacity, and 95% of magnet production, this restriction may cause production suspension risks. The industry is responding urgently, on the one hand, expanding the supply chain and adjusting inventory, and on the other hand, accelerating the research and development of non-rare earth technologies to reduce future dependence on Chinese resources.
Risk of Factory Shutdowns
The immediate consequence of China’s export restrictions is widespread anxiety within the automotive industry. Frank Eckard, CEO of German magnet manufacturer Magnosphere, warned that automakers and suppliers face an imminent risk of factory closures, with some plants potentially halting operations by mid-July 2025. The shortage of rare earth magnets threatens the production of critical components like EV motors. A single EV motor can require up to 2 kg of rare earth magnets.
China’s Dominance in Rare Earth Mining, Refining, and Magnet Production
China controls the core lifeline of the rare earth supply chain. In 2024, China’s rare earth oxide production will reach 240,000 tons, far exceeding Australia (18,000 tons) and the United States (15,000 tons). 90% of the world’s electric vehicle motors use neodymium iron boron magnets, and almost all of these magnets are produced in China, with leading companies such as TOPMAG dominating. This monopoly position allows China to influence global market prices and use export restrictions as a strategic bargaining chip.
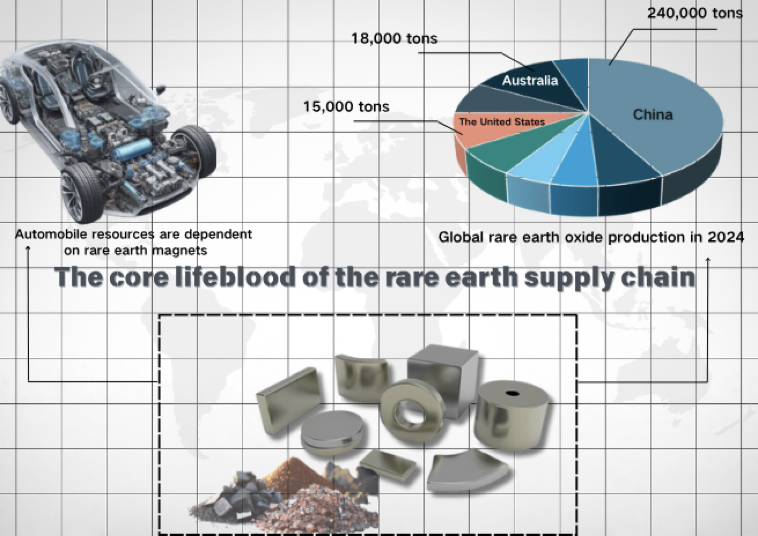
Development of Rare Earth-Free Magnet Technologies
The crisis is driving the rapid development of non-rare earth magnet technology. Several innovative technologies are expected to achieve the performance of NdFeB magnets while reducing costs and avoiding supply chain risks. Automakers and research institutions are stepping up efforts to find more sustainable alternatives that are not affected by geopolitics.
GE Aviation has developed a new rare earth-free dual-phase magnetic material that uses a high-temperature nitridation process to achieve a power density of 1.4 kW/kg and a peak efficiency of 94%, which is comparable to top-level NdFeB motors. Tests show that the material is resistant to high temperatures and mechanical stress, making it an ideal choice for electric vehicle motors.
Also Read: B Tech Electrical Engineering Syllabus: Course Structure
Ames National Laboratory has developed a new manganese-bismuth (MnBi) bonded magnet with outstanding high-temperature performance – the coercivity is nearly doubled at 100°C, which is particularly suitable for industrial motor applications. This technology is made through grinding MnBi powder and polymer coating to prevent magnetic loss, magnetic field orientation, and other processes. It also uses bismuth, a byproduct of lead and copper smelting, to reduce costs. Pump motor tests show that its performance not only meets the standards but also has excellent durability.
Niron Magnetics, backed by a $25 million investment led by Samsung Ventures and joined by General Motors and Stellantis, is developing “Clean Earth Magnets” based on iron nitride. These magnets offer high-temperature stability and environmental sustainability, using abundant iron instead of rare earths. With over $160 million in total funding, Niron is scaling up pilot production for automotive and consumer electronics markets.
A team at Texas A&M University has developed a rare earth-free motor using abundant materials like copper, focusing on efficiency, compactness, and sustainability. Simulations and prototype tests show performance comparable to NdFeB motors. The project, funded with nearly $500,000 and granted a U.S. patent, targets commercialization for EVs, wind turbines, and transportation systems. Using widely available materials could reduce production costs by 10-15% and mitigate environmental impacts from mining.
In India, Sterling Gtake E-Mobility Ltd (SGEM) has partnered with UK-based Advanced Electric Machines (AEM) to produce rare earth-free traction motors in Haryana. Targeting India’s growing EV market, AEM’s synchronous reluctance motor technology eliminates rare earths while maintaining high efficiency, supporting India’s “Make in India” initiative and reducing reliance on Chinese imports. Initial production focuses on two-wheelers and commercial vehicles, with plans to expand to passenger cars by 2028, aiming for a 10% share of India’s EV motor market.
Economic Benefits of Sustainable Local Materials
Rare earth-free technology has significant cost advantages because it uses abundant materials such as iron, copper, and bismuth, which are much cheaper than neodymium or dysprosium. This type of environmentally friendly material meets market demand and is expected to bring competitive advantages to leading automakers such as GM and Renault. Strong economic drivers are accelerating technology investment, and it is expected that global investment in research and development of rare earth-free vehicles will exceed US$2 billion by 2030.