In automation, not every component grab attention, but grippers literally do the grabbing. They’re the robotic fingers that handle, move, and position parts. And when it comes to choosing the right gripper for your application, it’s not just about what fits, it’s about what works best for your task, environment, and long-term efficiency.
Also Read: Tech Lokesh: A Creative Hub for Video Editing and AI Tools
Electric and pneumatic grippers dominate the market, and for good reason. They each bring their own strengths to the table, and knowing those strengths can help you cut downtime, boost precision, and get a lot more value from your setup.
But picking the wrong gripper? That can create a domino effect, poor part handling, maintenance headaches, or even quality defects. That’s why understanding which gripper suits your application isn’t a small technical decision, it’s a strategic one.
And if you’re working with a solution partner like Schunk India, you’re already a step ahead. With their wide range of smart gripping tech and real-world application support, they make sure you pick the right tools for the job, not just the trendiest.
Let’s break down the two options and find out what really makes one better than the other, and in which scenarios.
Electric Grippers: Precision, Control & Flexibility
Electric grippers aren’t just “fancier”, they’re engineered for applications where detail and control matter most. Unlike pneumatic models that work on compressed air, electric grippers use servo motors or stepper motors, giving users far more control over movement, grip force, and speed.
They offer some real standout benefits:
- Highly precise and programmable movement
- Adjustable grip strength and travel
- Real-time feedback on position and force
- Cleaner, quieter operation with no air hoses
- Integration-friendly with modern automation systems
If you’re handling electronics, fragile materials, or need adaptive part handling, electric grippers are where it’s at. You can easily switch parameters on the go, without stopping your line. That kind of flexibility is a game-changer for small batch sizes and complex assemblies.
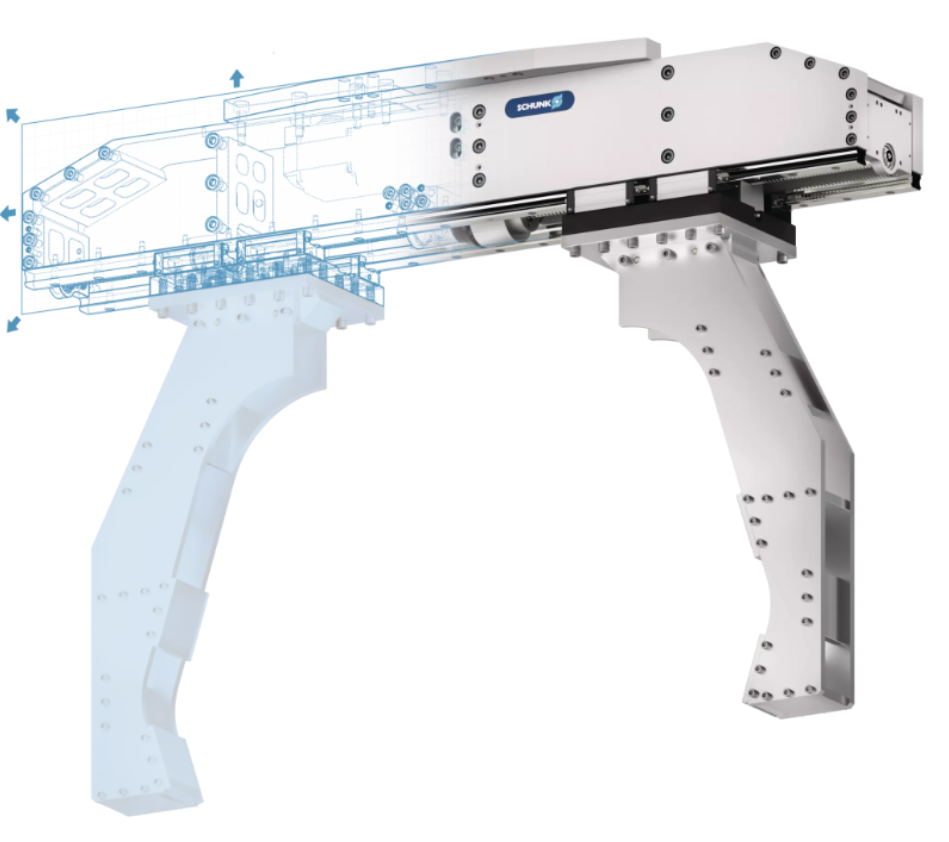
Schunk India’s electric grippers also come with smart sensors, modular build options, and simple setup with IO-Link or PLC controls. Whether you’re automating a lab or integrating with a cobot, they plug right in, no drama.
What’s more, they help reduce operational cost in the long run. Electric grippers only consume energy while moving, unlike pneumatic systems that need compressors running constantly. That’s great for sustainability and energy bills alike.
They’re also well-suited for cleanroom or hygienic environments, where air leaks or oil mist just aren’t acceptable. Think pharma, medical, and high-end electronics, where precision and cleanliness are deal breakers.
And when you’re aiming for smart manufacturing goals like predictive maintenance or digital feedback, electric grippers are already there, collecting data, responding in real time, and fitting neatly into your Industry 4.0 strategy.
Pneumatic Grippers: Simple, Fast & Cost-Effective
Pneumatic grippers, though less flashy, still dominate a massive chunk of industrial applications. Why? Because they’re fast, tough, and cost-effective. They work using compressed air to generate force, making them perfect for high-speed, repetitive tasks where consistency beats complexity.
Key benefits of pneumatic grippers include:
- Lightning-fast response time
- Rugged construction and long life
- Low initial cost and easy installation
- Suitable for harsh or dirty environments
- Minimal maintenance with basic upkeep
In auto plants, metal shops, and high-volume packaging lines, pneumatic grippers still rule. They can handle high loads with zero lag, and since they’ve got fewer moving parts, there’s less that can break.

Schunk India builds pneumatic grippers that can handle everything from small components to large industrial parts. Their designs are compact yet powerful, with protective seals and corrosion-resistant materials that hold up even in tough shop-floor conditions.
They also make sense when you’ve already got compressed air lines running, adding a gripper doesn’t require reengineering your whole setup. That’s often a big win for facilities trying to stay lean.
While they don’t offer much in terms of feedback or programmability, pneumatic grippers are ultra-reliable. And for simple open/close operations, they just get the job done, quickly and without complaints.
And yeah, while they might not fit into smart automation as seamlessly as electric versions, for many shops that’s totally fine. When your goal is speed and uptime, pneumatic systems still hold their ground well.
Comparing Electric vs. Pneumatic: Application Fit Matters
Alright, let’s get to the heart of it, how do you really choose between electric and pneumatic grippers?
Like most decisions in manufacturing, it depends. On the job, the environment, the scale, and your long-term automation goals.
Here’s a straight-up comparison to make things clearer:
Factor | Electric Grippers | Pneumatic Grippers |
Precision | High | Moderate |
Speed | Moderate | Very High |
Control | Full (programmable) | Basic (on/off) |
Feedback | Yes | No |
Setup | Digital-friendly | Air-based simple |
Cost (initial) | Higher | Lower |
Cost (long-term) | Lower | Higher (energy + upkeep) |
Environment | Clean, technical | Harsh, rugged |
If you’re in a high-mix, low-volume situation where you need precision, real-time adjustment, and system-level control, electric is a no-brainer.
If it’s a fast-paced, repetitive setup where speed and strength are key, pneumatic grippers might still be your best bet.
But here’s the twist: your shop might need both. And with modular gripper platforms like those from Schunk India, you can integrate electric for delicate handling and pneumatic for rugged tasks, in one cohesive system.
It’s not always a competition. Sometimes, it’s about combinations.
Smart Manufacturing and the Rise of Adaptive Gripping
Modern factories aren’t static. Products change, lines evolve, and new demands pop up faster than ever. That’s where adaptive, intelligent gripping comes into play, and electric grippers are leading the way.
In this smarter landscape, grippers are expected to do more than just grip. They:
- Automatically adjust to different shapes or weights
- Detect misalignment or slipping
- Share data with MES or cloud platforms
- Improve safety with force-sensitive controls
- Reduce downtime through predictive analytics
Schunk India’s electric grippers come built for smart environments. They connect, communicate, and collaborate, not just with robots, but with your entire production ecosystem.
Imagine a cobot-assisted line where one gripper handles multiple product types without a single tool change. Or a gripper that alerts your maintenance team before something fails. This is not a “someday” concept, it’s happening now, and it’s becoming the norm.
For manufacturers looking to future-proof operations, electric smart grippers are more than tools, they’re enablers of agility and insight. And in high-mix, low-volume manufacturing, that agility becomes your biggest competitive edge.
So, if you’re moving towards Industry 4.0 or already mid-journey, investing in smarter grippers should probably be on your roadmap, if it’s not already there.
Schunk India: A Trusted Partner in Gripping Technology
At the end of the day, tech is only as strong as the support behind it. That’s where Schunk India brings the edge.
They offer:
- A wide portfolio of electric and pneumatic grippers
- Custom solutions tailored for Indian industries
- Deep application engineering and technical support
- On-ground presence for faster implementation
- Training and after-sales that go the extra mile
With decades of global experience and deep regional expertise, Schunk understands both the complexity of high-end automation and the boots-on-ground needs of Indian manufacturers.
Whether you’re setting up a new line, upgrading legacy systems, or trying to meet new compliance or throughput goals, they’ll meet you where you are. And more importantly, help you get where you want to be.
Their product lineup is vast, but their approach is simple: build gripping systems that just work, day in and day out, without surprises.
Conclusion
Electric or pneumatic, choosing the right gripper isn’t just a technical decision. It’s about finding the balance between control and speed, cost and capability, present needs and future readiness.
Electric grippers offer flexibility, intelligence, and cleaner operation. They’re perfect for evolving environments, delicate handling, and smart integration. Pneumatic grippers, on the other hand, bring unmatched speed, toughness, and simplicity, still vital in many fast-paced industries.
With Schunk India, you’re not stuck choosing one over the other. You get expert insights, tailored solutions, and access to best-in-class gripping systems, backed by local support and deep industry understanding.
So before you pick a gripper, pick a partner who knows how to help you choose right. Because in automation, the grip might seem small, but it holds the whole process together.