In the modern industrial world, tech felts play a vital role in countless manufacturing and mechanical processes. These dense, non-woven fabrics are used in sectors ranging from automotive to textiles, construction to music, and many more. Whether you’re involved in machinery maintenance or soundproofing, these offer functional advantages like insulation, durability, and vibration dampening.
In this article, we’ll explore what these are, how they are made, their key properties, and the industries that rely on them daily. You’ll also find a helpful table showcasing their different applications. Let’s dive into this essential industrial material and understand why these are so important.
Read More About Tech and Health at Aiotechnical.com
What Are Tech Felts?
These—short for technical felts—are specially engineered felts designed for industrial and technical use. These felts are created using either natural fibers such as wool or synthetic materials like polyester, acrylic, or aramid fibers.
Manufacturers design them to be strong, flexible, and resistant to heat, pressure, and moisture. Their structure helps them absorb shock and noise, making them ideal for use in machines and insulation systems. The production of tech felts usually involves wet felting or needle punching, processes that compress and lock fibers into a solid, felted mass.
Also Read: Global Village Tech Park: A Thriving IT Hub in Bengaluru
How These Are Manufactured
The manufacturing process of these depends on their intended use. Two main techniques are used—wet felting and needle punching.
In wet felting, fibers are exposed to moisture, heat, and agitation. This causes them to mat and shrink, forming a strong, uniform material. In needle punching, barbed needles punch through layers of fibers, entangling them into a durable sheet. This technique is often used for synthetic fibers and is suitable for higher-volume production.
The end result is a tough, thick material that can be cut, shaped, or molded to fit a wide range of industrial applications. These felts can be tailored by thickness, density, color, and fiber type, depending on the specific industrial needs.
Characteristics
These are more than just simple fabric. They are designed to meet strict performance standards in industrial environments. Let’s explore their core features:
- High Durability: They resist wear, making them ideal for machinery and automotive components.
- Thermal Resistance: They can handle high temperatures, useful in engines or industrial ovens.
- Moisture Absorption: These felts can absorb oils and water without getting soggy.
- Vibration Dampening: They reduce machinery noise and mechanical vibrations.
- Flexibility: They can be easily shaped and adjusted for specific industrial equipment.
Because of these features, these have become a go-to material in multiple industries.
Industrial Applications of Tech Felts
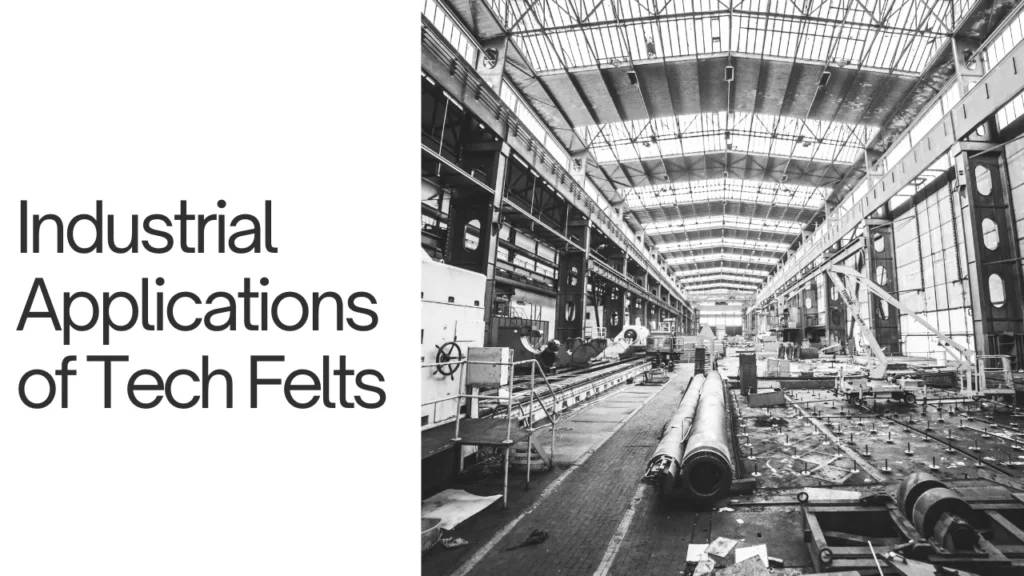
These are widely used across sectors due to their adaptable nature. Here’s a detailed look at where these felts are commonly applied.
Industry | Application | Purpose |
---|---|---|
Automotive | Padding, insulation, gaskets | Reduces noise, heat, and vibration |
Construction | Soundproofing, thermal insulation | Blocks sound and retains temperature |
Textile Machinery | Spacer felts, heat guards | Prevents friction and protects parts |
Musical Instruments | Piano hammers, drum pads | Improves sound and dampening |
Aerospace | Insulation, seals, shock absorbers | Handles high pressure and temperatures |
Furniture | Underlays, padding | Provides cushioning and shape support |
Oil & Gas | Sealing pads, filters | Resists chemical exposure and wear |
As shown in the table, these are valued for both their versatility and technical efficiency.
Why Businesses Rely on These
Every factory, production plant, or workshop that depends on machinery will likely use these in some way. Businesses prefer these because they are easy to install, cost-effective, and reduce long-term maintenance costs. Their ability to extend machinery life by reducing friction and vibration is crucial in high-usage industrial environments.
In construction, these help insulate homes and buildings. They trap sound and regulate temperature more effectively than many alternatives. In musical instrument manufacturing, these are used for tone control and noise dampening. Even in luxury furniture, these felts are used as cushioning materials.
Also Read: Reliable Tech Park: A Hub for Businesses in Navi Mumbai
Environmental Effect and Sustainability
Modern production techniques are moving toward eco-friendly felts. Manufacturers now offer options made from recycled materials or natural fibers. Wool felts, for example, are biodegradable and offer excellent thermal and acoustic insulation. Many industries are also moving away from harsh chemical treatments to make these more sustainable.
Choosing eco-conscious these not only supports environmental goals but also reduces the carbon footprint of the industries that rely on them.
In Pakistan and Other Emerging Markets
In countries like Pakistan, demand for these is rising due to rapid industrial growth. The textile, automotive, and construction industries have seen a growing need for heat and sound insulation materials. Companies are importing advanced felts or establishing local production units to meet the demand.
Pakistani industries often use these in textile machinery as cushioning between fast-moving parts. The use in local automobile manufacturing is also increasing, particularly for soundproofing and interior padding.
Types Based on Fiber
There are various kinds of these depending on the fiber used. Each type has its own benefits.
Felt Type | Material | Key Benefits |
---|---|---|
Wool Felt | Natural wool | Biodegradable, good insulation |
Polyester Felt | Synthetic polyester | Cost-effective, moisture resistant |
Acrylic Felt | Synthetic acrylic | Lightweight, colorful, and soft |
Aramid Felt | Kevlar, Nomex fibers | Fire-resistant and heat-tolerant |
Blended Felt | Wool + synthetic mix | Combines strength and flexibility |
Understanding these types helps industries pick the right these for specific functions.
The Manufacturing Process Behind These
These are specially engineered non-woven materials used in a wide range of industries. From automotive to construction, their importance lies in their durability, insulation capabilities, and vibration resistance. The manufacturing of these involves a detailed and controlled process that transforms raw fibers into thick, dense sheets. These felts are designed to perform specific technical functions, and the production methods reflect this level of precision and customization.
Fiber Selection: The Foundation of These
The first step in manufacturing these begins with selecting the right fibers. Manufacturers choose from natural fibers like wool or synthetic fibers such as polyester, acrylic, or aramid (e.g., Kevlar, Nomex). The type of fiber directly impacts the performance of the final felt. For example, wool offers superior thermal and acoustic insulation, while aramid fibers are ideal for high-temperature applications.
Blended felts are also common, combining natural and synthetic fibers to balance durability, flexibility, and cost. The fibers are cleaned and combed before entering the felting process.
Carding and Layering
Once the fibers are ready, they go through a carding machine. This machine aligns the fibers in one direction, creating a web-like layer. The fibers are then layered on top of one another to reach the desired thickness. This stage ensures the even distribution of fibers, which is essential for uniform density and strength across the entire felt sheet.
The number of layers varies based on the end-use. Thicker felts used in heavy machinery will have more fiber layers than lightweight felts used in musical instruments or furniture.
Felting Techniques: Wet Felting and Needle Punching
These are formed using one of two primary methods: wet felting or needle punching. Each method has its own advantages and is chosen based on the application and fiber type.
Wet Felting
In this method, the fiber layers are exposed to moisture, heat, and pressure. As the material is agitated, the fibers interlock and shrink, forming a dense and durable mat. Wet felting is ideal for wool-based felts and provides a smooth, compact surface. This technique has been used for centuries and is still favored for specific technical applications.
Needle Punching
Needle punching is a mechanical method where barbed needles repeatedly punch through the fiber layers, tangling the fibers into a solid sheet. This process is used mainly for synthetic felts and offers greater control over thickness and density. Needle-punched felts are common in automotive and industrial sealing applications where strength and consistency are vital.
What’s Coming In Tech Felts
The future of these looks promising, especially as industries seek smarter materials that are lighter, stronger, and more sustainable. Innovations like nanofiber felts and felts with embedded sensors are already being explored. These advanced versions could be used for predictive maintenance, monitoring machine performance in real-time.
As manufacturing becomes more automated and efficient, the role of these will expand further. From smart textiles to hybrid materials, these felts are evolving beyond basic use and into high-performance industrial solutions.
Also Read: B.Tech Food Technology: Course and Career Opportunities
Final Thoughts
Tech felts may not grab headlines, but they are everywhere. From the padding inside your car door to the felt lining your washing machine motor, this versatile material makes a big impact. Its ability to adapt to heat, pressure, moisture, and vibration makes it an irreplaceable asset across industries.
Whether you’re an engineer, a manufacturer, or a curious reader, understanding the value of these can open your eyes to their quiet but powerful role in our modern world. As innovation continues, so will the range of applications for this essential material.
These are not just fabric—they’re the backbone of industrial reliability, efficiency, and innovation.